Metal cutting machines – Metal laser cutting machines – Metal sheet laser cutting machines
XT Laser – Metal Sheet Laser Cutting Machine
Metal cutting machines are sometimes referred to as metal laser cutting machines, as most metal cutting processes now use laser cutting machines to replace traditional processes. Therefore, there are only some differences in terms of terminology. The reason why metal cutting machines are popular is mainly because metal materials that were previously difficult to process are increasingly being used, With the development of technology, traditional metal sheet processing methods can no longer meet modern production needs. The emergence of metal sheet laser cutting machines has brought revolutionary changes to metal material processing methods.
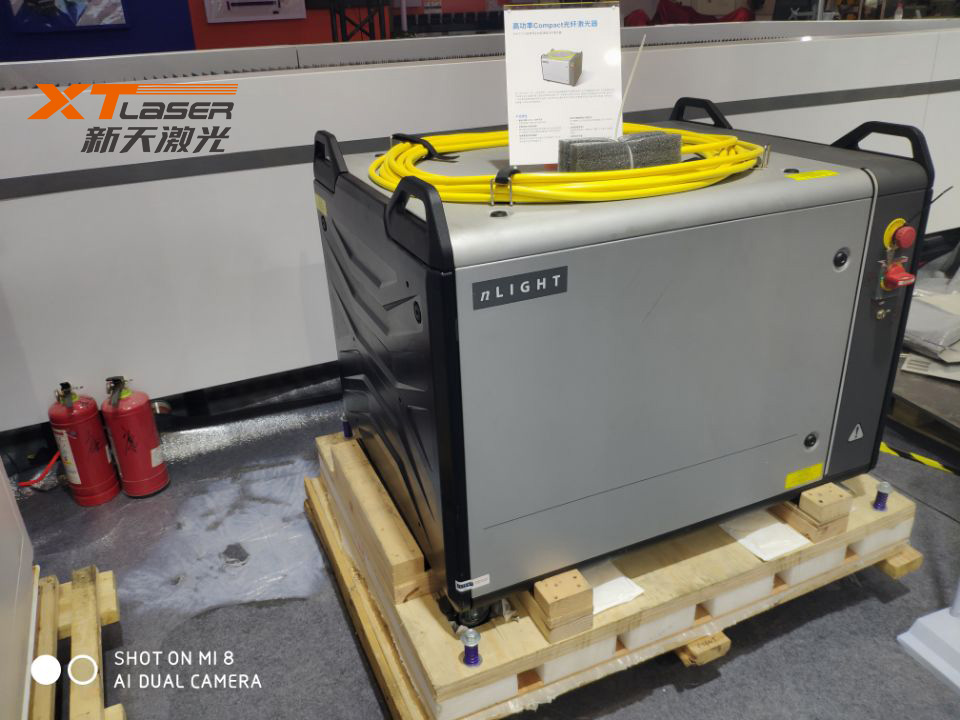
Metal cutting is an important production process in the industrial construction industry and other fields. Metal cutting machines, also known as metal laser cutting machines, or metal sheet laser cutting machines, release energy when the laser beam is irradiated on the surface of the metal workpiece to melt and evaporate, in order to achieve the purpose of cutting or carving. They have high accuracy, fast cutting, are not limited to cutting pattern limitations, automatic typesetting saves materials, and smooth cuts, Low processing cost and other characteristics.
It is understood that the new generation of advanced laser cutting systems have good optical modes, small cutting seams, and high accuracy; The mechanical follow-up cutting head directly contacts the sheet metal for movement, and the laser focus remains unchanged. The cutting speed and quality are uniform and consistent throughout the entire working surface; Adopting dual guide rail positioning and ball screw transmission, it has fast speed, high accuracy, smooth movement, good dynamic performance, and long service life; The machine tool is equipped with over travel anti-collision limit switches and polyurethane anti-collision stop bars in both vertical and horizontal movement directions, ensuring maximum safety during machine operation; The automatic programming system directly generates machining programs from graphic files, and the computer simulates the machining path of graphics, improving the efficiency of machining and material utilization.
Metal cutting machines, as a new type of tool, are increasingly being used in various industries. So how is laser cutting used and how can the quality of laser cutting be distinguished?
Firstly, the energy of the laser is concentrated in the form of light into a high-density beam, which is transmitted to the working surface to generate sufficient heat to melt the material. In addition, the high-pressure gas coaxial with the beam directly removes the molten metal, thereby achieving the purpose of cutting. This indicates that laser cutting processing is fundamentally different from machine tool mechanical processing.
It utilizes a laser beam emitted from a laser generator, which is focused into a high-power density laser beam through an external circuit system. The laser heat is absorbed by the workpiece material, and the workpiece temperature rises sharply. After reaching the boiling point, the material begins to vaporize and form holes. As the beam moves relative to the workpiece, the material eventually forms a slit. The process parameters (cutting speed, laser power, gas pressure, etc.) and motion trajectory during slitting are controlled by the CNC system, and the slag at the slot is blown away by auxiliary gas at a certain pressure.
During the laser metal cutting process, auxiliary gases suitable for the material being cut are also added. During steel cutting, oxygen is used as an auxiliary gas to produce exothermic chemical reactions with molten metal to oxidize the material, while also helping to blow away the slag inside the grid. For metal parts with high processing accuracy requirements, nitrogen gas can be selected as an auxiliary gas in industry.
Many metal materials, regardless of their hardness, can be cut without deformation using a metal sheet laser cutting machine (currently, the most advanced metal laser cutting machine can cut industrial steel with a thickness of nearly 100mm). Of course, for high reflectivity materials such as gold, silver, copper, and aluminum alloys, they are also good heat transfer conductors, making laser cutting difficult or even impossible (some difficult to cut materials can be cut using a pulse wave laser beam, as the extremely high peak power of the pulse wave can instantly increase the material’s absorption coefficient of the beam).