Application and development trend of laser cutting machine
XT Laser-laser cutting machine
The laser cutting machine is widely used, and the laser processing technology will be the golden period of development in the next 30-40 years. There are many factors to consider when selecting the laser cutting machine. In addition to considering the maximum size, material quality, the maximum thickness to be cut and the width of raw materials, more attention should also be paid to the future development direction.
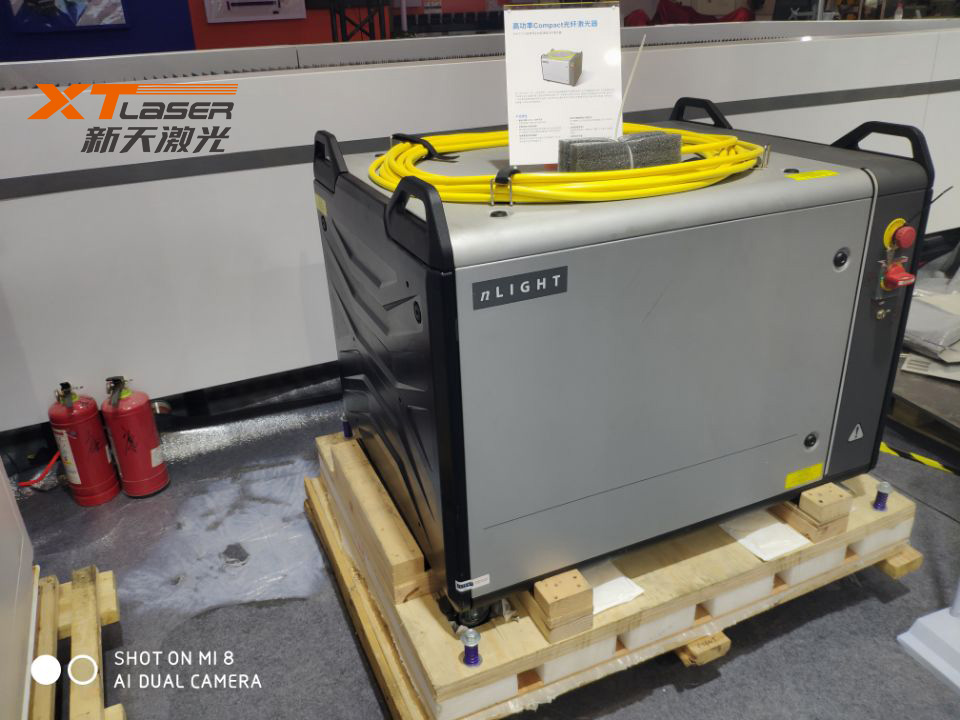
Laser cutting is a technological revolution in sheet metal processing and the “processing center” of sheet metal processing. Laser cutting has the advantages of high flexibility, fast cutting speed, high production efficiency, short production cycle and so on, and has gained higher economic value for customers. Laser cutting machine has no workpiece deformation due to non-contact laser cutting. No tool wear, and good adaptability for cutting various metal materials; Both simple and complex parts can be accurately and rapidly formed and cut by laser cutting machine. The cutting seam is narrow, the cutting quality is good, the degree of automation is high, the operation is simple, the labor intensity is low, and there is no pollution; It can realize automatic layout, improve material utilization rate, low production cost and good economic benefits. The equipment has long service life and high use value. At present, most of the plates with a thickness of more than 2mm in foreign countries use laser cutting machines. Many foreign experts agree that the next 30-40 years will be a golden period for the development of laser processing technology (the development direction of sheet metal processing).
Generally speaking, it is recommended to use laser cutting to cut carbon steel plate within 20mm, stainless steel plate within 10mm and non-metallic materials, such as acrylic acid and wood. Plasma cutting is recommended for 20-50mm steel plate, and flame cutting is recommended for thicker steel plate. When processing copper, aluminum and other highly reflective laser materials, as well as fragile non-metallic materials such as glass and marble, the water knife is used for cutting. Manufacturers on the chassis and cabinet within 1mm use a large number of CNC punches with relatively single variety in the sheet metal processing industry, and coordinate with other cutting methods to cut.
First, as the mainstream of traditional laser cutting machines, CO2 laser can stably cut carbon steel within 20mm, stainless steel within 10mm and aluminum alloy below 8mm; Secondly, fiber laser has obvious advantages in cutting thin plates within 4mm, while its quality is poor due to the influence of solid laser wavelength when cutting thick plates. Laser cutting machine is not omnipotent. The wavelength of CO2 laser is 10.6 um, and that of solid-state laser such as YAG or fiber laser is 1.06 um. The former is easier to be absorbed by nonmetals and can cut high-quality wood, acrylic acid, polypropylene, plexiglass and other nonmetallic materials. However, the latter is not easy to be absorbed by nonmetals and cannot cut nonmetallic materials. However, when high reflective materials such as copper, silver and pure aluminum are encountered, both lasers have no choice.
With the rapid development of laser technology and the continuous improvement of production technology, laser cutting, as a precision blanking equipment, is quietly replacing the traditional stamping and cutting equipment. In the face of the dazzling laser cutting machines and the casual boasting of some businesses, the buyers of laser cutting machines are even more confused. Han’s Superpower put forward the following opinions on the selection of laser cutting machine:
From the application field of laser cutting machine and the technical requirements put forward by users, the future development direction of laser cutting machine is undoubtedly high power, large format, high efficiency, one-time molding and high intelligence. Widely used in locomotive industry and heavy industry, it has brought high efficiency and high quality production capacity to users. High-speed and high-precision laser cutting machines are widely used in construction machinery and high value-added products. As an external processing industry, the cantilever laser cutting machine with high cost performance is the best choice.
In addition, the robot fiber laser flexible processing system has a long history and application in the automobile industry and its supporting industries. It was previously monopolized by foreign integrators. In recent years, due to the financial crisis and the continuous improvement of production technology in the automobile industry, the 3D five-axis laser cutting machine has been constantly updated, and the mystery of foreign ultra-high prices has been unveiled. In recent years, auto body-in-white welding, auto instrument panel laser weakening, auto airbag laser welding, auto bumper, door, center pillar and other robot flexible cutting machines, auto bumper laser welding, auto exhaust pipe online welding system, auto shift sleeve laser automatic cutting equipment, etc. have been provided to auto users. From the 24-hour stable and efficient production of user websites, it can be seen that domestic enterprises have certain strength.
There are many factors to consider when selecting laser cutting machine. In addition to considering the maximum size, material quality, maximum thickness to be cut and the size of raw material width, more attention should also be paid to the future development direction, for example, the maximum size of the workpiece to be processed after the technical transformation of the manufactured product, that is, the width of the material provided by the most economical material steel market is the own product, loading and unloading time, etc. Laser cutting machine is a modern equipment with high input and high output. Every minute saved may mean an extra 10 yuan. At the same time, the current situation of laser cutting machine is also the focus that the buyer of laser cutting machine must pay attention to. The fierce market competition must avoid homogeneous competition as much as possible.
For railway locomotive, heavy industry, construction machinery and other industries, the contour of the parts to be processed is not too complex. In order to improve the processing capacity and efficiency, it is recommended to use the large-format series, which is generally 3-4.5 meters wide and 6-30 meters long, to realize the one-time processing of medium and thick plates, and save time and materials. When there are a large number of workpieces with thickness more than 20 mm, plasma cutting equipment (thickness more than 45 mm plus flame cutting) is the best choice. It is suitable for processing 3-50mm or even thicker steel plates. Feeding and cutting are carried out at the same time. Cutting thin and thick plates at the same time will greatly improve the processing efficiency. For some small workpieces, high-speed and high-precision series is the best choice.