Metal fiber laser cutting problem and solution – Alex
Metal fiber laser cutting main use high temperature gasify metal material and blow the gas away under the help of inert gases. Compared with traditional cutting process, it have very high precision and fast cutting speed. At the same time, its loss rate is very low, so it have more and more wide application.
Due metal fiber laser cutting process, also we will face many different problems, follows is some common problems and solution. It can help us use this machine better.
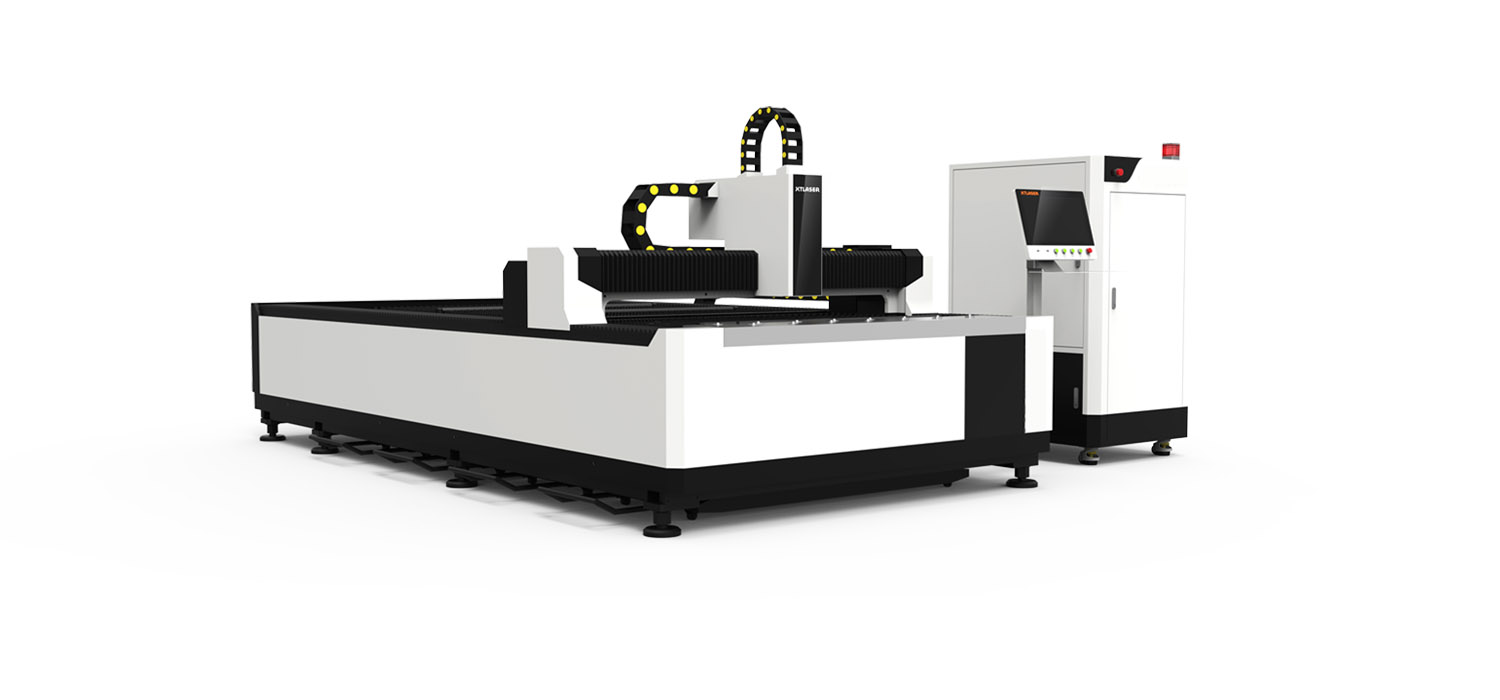
Erosion on the sharp corners
When fiber laser cutting machine cut sharp corner, laser will turn to another side when finish one side. During this process, laser head will become ZERO then back to normal speed. Laser will stay on the corner parts for long time but laser power keep working. Due to the heat radiating area is very small near the corner so the corner temperature will be very high and metal will be melt. So the corners parts is not smooth.
Laser can’t cut through the metal
The most common reason is laser generator power attenuation so that the power is not enough to cut through the plate.
Additional, so high cutting speed, focus lens broken, laser path and voltage problems are common reason cause this problem.
Of course, material problems, auxiliary gas low pressure, water cooling system also may can rise this problem.
No laser output
Follow reason may cause this problem.
- laser generator is aged so the laser power become weak.
- Electric current is not enough so that the laser output is weak.
- Too many dust in the laser generator, it may pollute optical parts and laser light can’t go through.
- Laser power supply don’t work but cooling system keep working so that some parts freeze.
Cutting process is discontinuous
Due metal fiber laser cutting process, discontinuous cutting is very common. Usually it will bring large waste for our work.
Unreasonably program is the most common reason to rise this problem. Metal fiber laser cutting need close to the cutting surface. When we cut many different parts on one plate, program select lineation first then cutting acquiescently. It can avoid laser cutting head crash the cut parts and broken laser cutting head. When we white the program if some position is not closed, laser cutting will be discontinuous.
Also, change auxiliary gas during cutting process also may cause this problem. We know auxiliary gas will blow away the gasified metal, when we continue cutting the same parts after change gas, the position may be little different with finished position.
In this case, how we can avoid these problem? Next items we will discuss how to avoid these problems.
Contact Information:
Alex Wang
Email: xintian104@xtlaser.com
Skype: saint512406
Mobile&whatsapp : 0086 18766152065
Web: www.xtlaser.com