What are the focal points of laser cutting machines and what are the differences?
XT Laser Plate and Tube Integrated Laser Cutting Machine
Laser cutting uses a focused high-power density laser beam to irradiate the workpiece, rapidly heating the material to the gasification temperature and evaporating to form holes. When the beam of light moves to the material, a hole with a narrow width (such as about 0.1mm) is continuously formed to complete the cutting of the material.
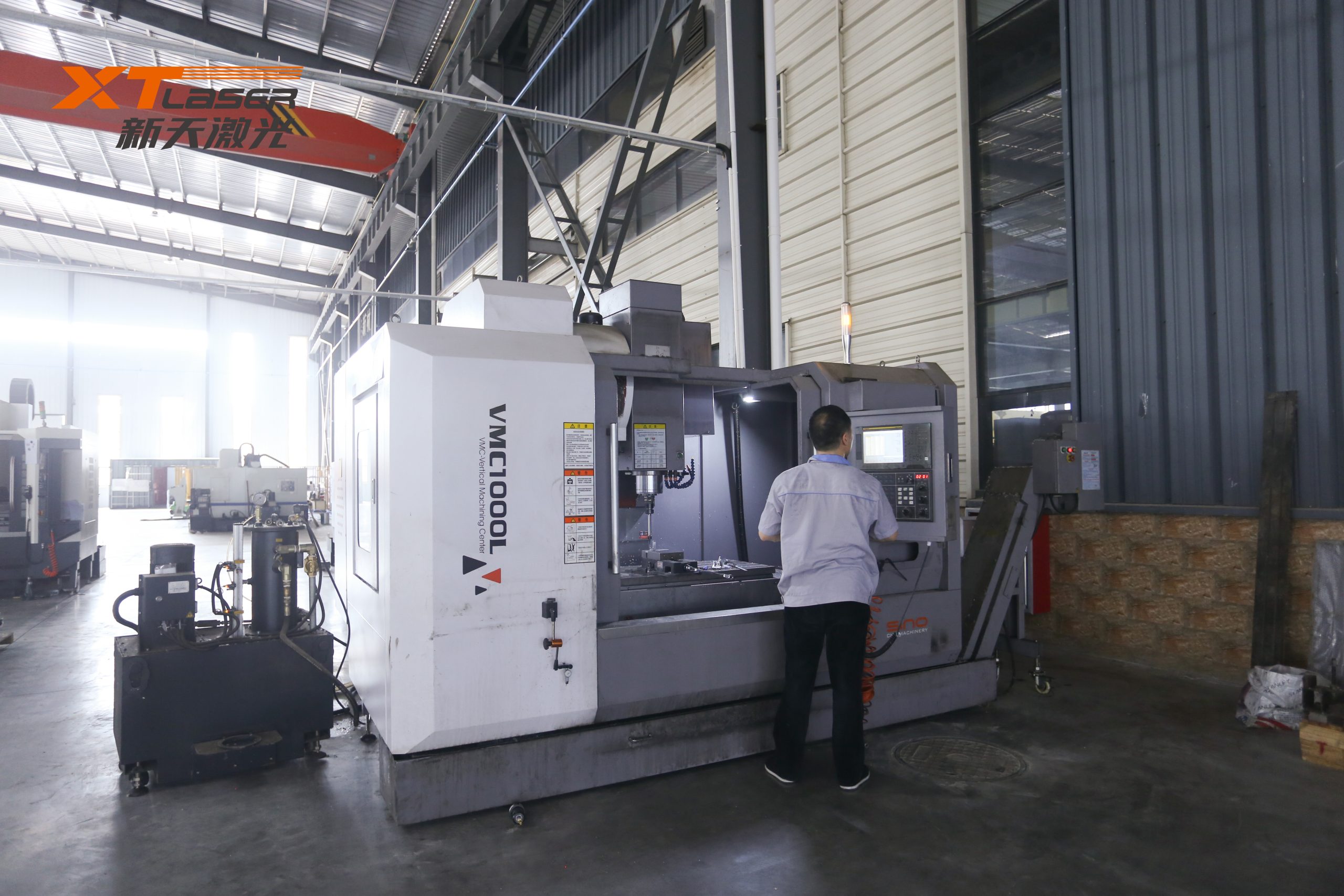
During laser cutting, there is no contact between the welding torch and the workpiece, and there is no tool wear. To process parts of different shapes, there is no need to change the “tool”, only the output parameters of the laser need to be changed. The laser cutting process has low noise, low vibration, and no pollution. Compared with other thermal cutting methods, the general characteristics of laser cutting are fast cutting speed and high quality.
So, what are the focal points of laser cutting machines? Any difference? Today, XT Laser will talk about the three key relationships of laser cutting machines.
Focus position and difference analysis of laser cutting machine:
Laser cutting can be divided into four categories: laser vaporization cutting, laser melting cutting, laser oxygen cutting, and laser scribing and controlled fracture. Laser cutting is one of the thermal cutting methods. The laser cutting machine is a technological revolution in sheet metal processing and a “machining center” in sheet metal processing. The laser cutting machine has high flexibility, fast cutting speed, high production efficiency, and short product production cycle, which has won a wide market for customers.
The focus position of the laser cutting machine is on the surface of the workpiece.
This is the most common focusing position, also known as 0 focal length, commonly used for cutting SPC/SPH/SS41 and other workpieces. When using, keep the focus of the laser cutting machine close to the surface of the workpiece. At this focal point, due to slight differences in the smoothness of the upper and lower surfaces of the workpiece, the cutting surface on the side near the focal point will be smoother, while on the contrary, the cutting surface on the side further away from the focal point will be rougher. In practical use, it is often determined based on the different process requirements of the upper and lower surfaces.
The focus position of the laser cutting machine is inside the workpiece.
The focus position inside the workpiece is called the positive focal length. When cutting materials such as stainless steel or aluminum steel plates, the focus method is generally used to make the cutting focus located inside the workpiece. The main disadvantage is that the cutting range is relatively large, and this mode often requires stronger cutting airflow, sufficient temperature, and longer cutting and perforation time. Therefore, it is only used when cutting hard materials such as stainless steel or aluminum.
3. The focus position of the laser cutting machine is on the workpiece.
The focus position on the workpiece is called negative focal length, because the cutting point is located neither on the surface of the workpiece nor inside the workpiece, but above the cutting material. When the focus position is on the workpiece, it is because the thickness of the plate is relatively high. If the focus is not positioned in this way, the oxygen delivered by the nozzle may be insufficient, resulting in a decrease in cutting temperature and inability to cut the material. But there is a significant disadvantage that the cutting surface is rough and not suitable for precision cutting.
The above is the focus position and difference analysis of the laser cutting machine. During the process of using a laser cutting machine, different focusing modes can be selected according to the processing needs of different workpieces, which can fully utilize the performance advantages of the laser cutting machine and ensure the cutting effect. Laser is the use of material excitation to generate light, which has a strong temperature. When in contact with materials, it can quickly melt on the surface of the material, form holes, and cut according to the movement of the alignment points. Therefore, compared to traditional cutting methods, this cutting method has smaller gaps and can save most of the material. However, based on the definition and analysis of cutting effect, the material cut by laser is analyzed, Its cutting effect is satisfactory and its accuracy is high, which inherits the advantages of laser and cannot be compared to ordinary cutting methods.