Comparison between laser cutting and traditional sheet metal cutting
XT Laser – Laser Cutting Machine
Traditional sheet metal processing
Because (CNC) cutting machines mainly use linear cutting, although they can cut 4-meter-long sheets, they can only be used for sheet metal processing that only requires linear cutting. Generally used in industries that only require linear cutting, such as cutting after flattening.
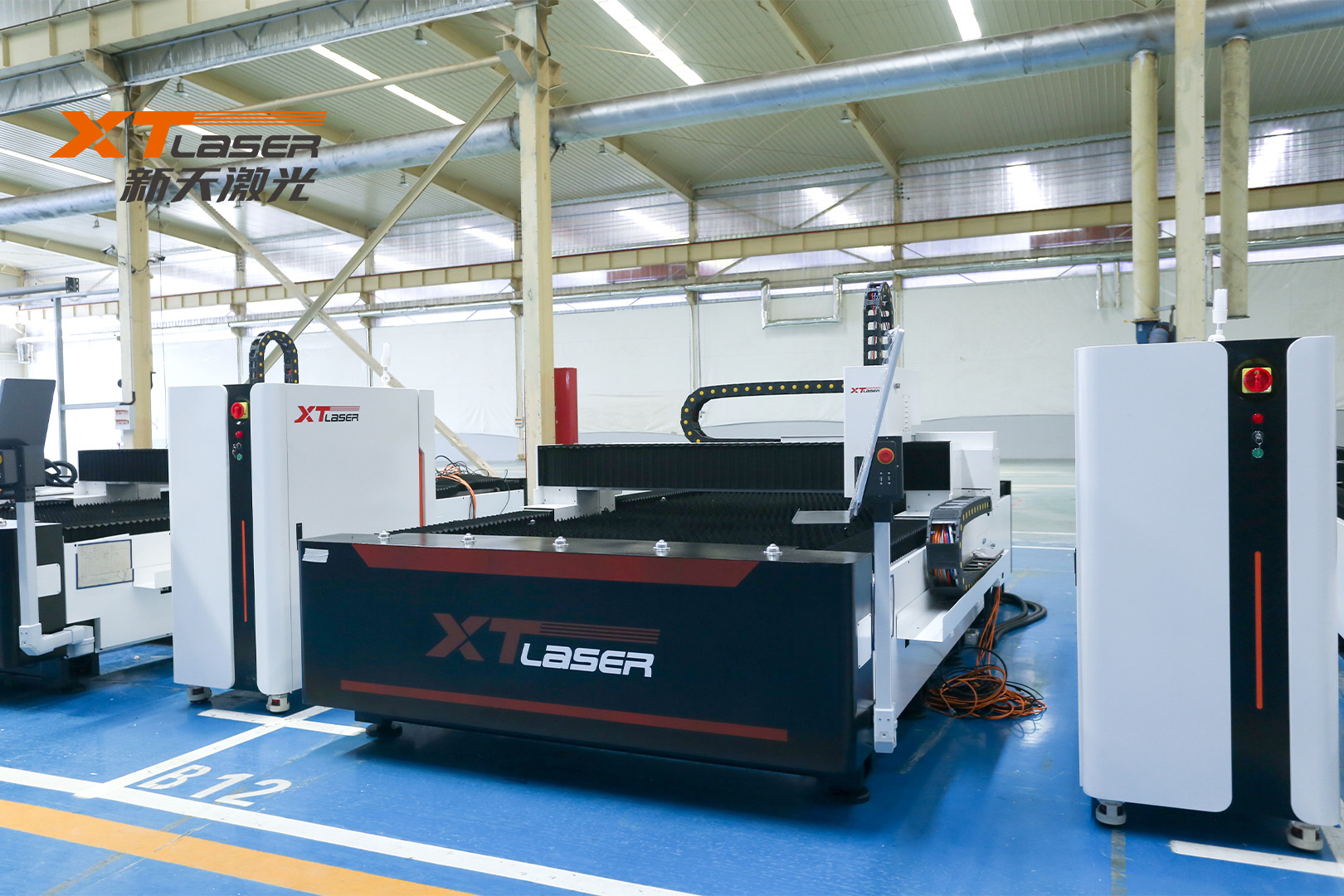
CNC/turret punch machines have greater flexibility in curve machining. A punching machine can have one or more sets of square, circular, or other special requirements of punching machines, which can process specific sheet metal workpieces at once, most commonly in the chassis and cabinet industry. The processing technology required for them is mainly the cutting of straight, square, and circular holes, with relatively simple and fixed patterns. The advantage is simple graphics and fast processing speed of thin plates, while the disadvantage is limited punching ability for thick steel plates. Even if punching is possible, the surface of the workpiece will still collapse, which requires a mold. The mold development cycle is long, the cost is high, and the degree of flexibility is not high enough.
Flame cutting, as a primitive traditional cutting method, used to have low investment and low requirements for processing quality. If the requirements are too high, it can be solved by adding a mechanical processing process, which has a very large quantity in the market. Now mainly used for cutting thick steel plates over 40mm. Its disadvantages are excessive thermal deformation during cutting, too wide incision, waste of material, slow processing speed, and only suitable for rough machining.
High pressure water cutting is the use of high-speed water jets mixed with diamond sand to cut plates. It has almost no restrictions on materials, and the cutting thickness can almost reach over 100mm. It is also suitable for materials that are prone to cracking during thermal cutting, such as ceramics and glass. It can be cut, and materials such as copper and aluminum that have strong laser reflectivity can be cut with a water jet, but laser cutting has significant obstacles. The disadvantage of water cutting is that the processing speed is too slow, too dirty, not environmentally friendly, and the consumables are also high.
Plasma cutting and fine plasma cutting are similar to flame cutting. The Heat-affected zone is too large, but the precision is far higher than flame cutting. The speed also has an order of magnitude leap, becoming the main force in plate processing. The actual cutting accuracy limit of the top domestic CNC fine plasma cutting machine has reached the lower limit of laser cutting, and the cutting speed of 22mm carbon steel plate has reached over 2 meters per minute. The cutting end face is smooth and flat, with the best slope. Control the temperature within 1.5 degrees. The disadvantage is that the thermal deformation is too large and the slope is large when cutting thin steel plates. In situations where precision is required and consumables are relatively expensive, it is powerless.
Laser processing has the following characteristics:
1. The laser power density is high, and the temperature of the material rapidly rises, melts or vaporizes after absorbing the laser. Even materials with high melting points, high hardness, and brittleness can be processed by laser.
2. There is no contact between the laser head and the workpiece, and there is no problem of tool wear.
3. The workpiece is not affected by the machining chip force.
4. The diameter of the laser beam spot can be as small as micrometers, and the action time can be as short as nanoseconds and picoseconds. At the same time, the continuous output power of high-power lasers can reach the order of kilowatts to tens of thousands of watts, so lasers are suitable for precision micro processing and also for large-scale sheet metal processing.
5. The laser beam is easy to control. Combined with precision machinery, precision measurement technology, and electronic computers, it can achieve high automation and precision in processing.
Laser cutting is a technological revolution in sheet metal processing and a “machining center” in sheet metal processing. Laser cutting has high flexibility, fast cutting speed, high production efficiency, and short product production cycle, which has won a wide market for customers. Laser cutting has no cutting force and does not deform during the processing. No tool wear, good material adaptability. Both simple and complex parts can be cut by laser for precise rapid prototyping. The cutting seam is narrow, the cutting quality is good, the degree of automation is high, the operation is simple, the labor intensity is low, and there is no pollution. It can achieve automatic material cutting and layout, improve material utilization, reduce production costs, and have good economic benefits. This technology has a long effective lifespan.