Advantages and disadvantages of plate laser cutting machine compared with traditional processing technology
XT Laser-sheet machine light cutting machine
With the rapid development of sheet metal processing technology, domestic processing technology is also constantly updated and iterative. In the application of sheet metal cutting, cutting equipment mainly includes (NC and non-NC) plate shears, punches, flame cutting, plasma cutting, high-pressure water cutting, laser cutting, etc. Sheet metal cutting has a wide range of applications, such as heavy machinery, ships, clothing, glass and other industries. Improving the utilization rate of sheet metal can reduce the production cost of enterprises and bring considerable economic benefits to enterprises.
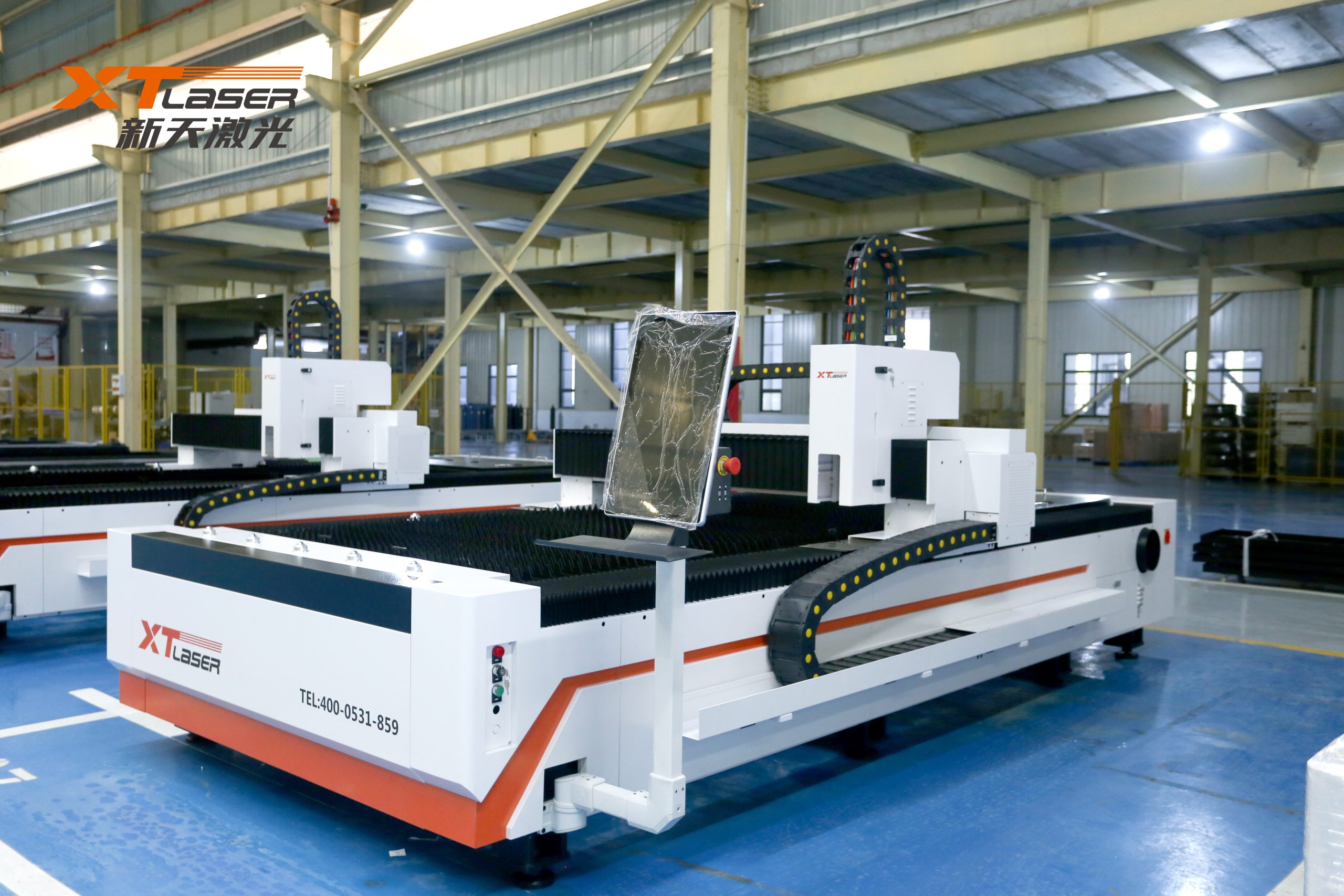
For sheet metal processing, laser cutting technology is a very advanced cutting technology, which can greatly improve labor productivity. In the process of sheet metal processing, the application of laser cutting machine can effectively shorten the processing cycle, improve the processing accuracy, and save all kinds of replacement stamping dies when high-precision machining highly complex parts. These advantages have been adopted by many manufacturers. Enterprises attach importance to and begin to actively use laser cutting machines for sheet metal processing.
The disadvantages of traditional technology.
The traditional cutting process, such as numerical control plate shears, can only be used for linear cutting. Compared with the multi-function operation of the fiber laser cutting machine, it has a disadvantage that cannot be ignored. Although the investment of flame cutting is low, the thermal deformation is too large when cutting thin plates, which affects the cutting quality of materials and wastes materials. It is not as fast as the fiber laser cutting machine. But for thick plate cutting, flame cutting still has advantages. The precision of plasma cutting is higher than that of flame cutting, but when cutting thin plates, the thermal deformation is large and the inclination is large. Compared with the precision cutting of laser cutting machine, it is easy to waste raw materials. High-pressure water cutting has no restrictions on materials, but compared with fiber laser cutting machine, its speed is too slow and consumption is high.
Metal sheet laser cutting machine
For a long time, the mechanical processing industry has been applied in many industries because of its light weight, high strength, good conductivity (can be used for electromagnetic shielding), low cost, and good batch production performance. What are the advantages of fiber laser cutting machine compared with traditional metal cutting?
(1) Use programming software to improve laser cutting efficiency. Laser cutting can effectively use the advantages of programming software, greatly improve the utilization rate of sheet materials, reduce the use and waste of materials, and reduce the labor intensity and intensity of workers to achieve the desired results. On the other hand, optimizing the layout function can eliminate the blanking link of sheet cutting, effectively reduce the clamping of materials and reduce the auxiliary processing time. Therefore, it promotes a more reasonable arrangement of the blanking scheme, effectively improves the processing efficiency and saves materials.
(2) Save product development cycle and realize mass production of sheet metal parts. In the growing market environment, the speed of product development means the market. The application of laser cutting machine can effectively reduce the number of molds used, save the development cycle of new products, and promote the speed and pace of its development. The quality of parts after laser cutting is good, and the production efficiency is significantly improved, which is conducive to small batch production, and effectively ensures the market atmosphere in which the product development cycle is increasingly shortened. The application of laser cutting can accurately locate the size of the blanking die, laying a solid foundation for future batch production.

(3) Reduce sheet metal processing procedures and production costs. In the sheet metal processing operation, almost all the plates need to be formed on the laser cutting machine at one time and welded together directly. Therefore, the application of the laser cutting machine reduces the process and construction cycle, and has high work efficiency, which can realize the dual optimization and reduction of labor intensity and processing costs, and at the same time promote the optimization of the working environment, greatly improve the research and development speed and progress, reduce mold investment, and effectively reduce costs.