Advantages of laser cutting machine processing technology
XT Laser-laser cutting machine
1. Process introduction
Laser cutting is a non-contact process with high energy density and good controllability. It focuses the laser beam on the spot with the minimum diameter less than 0.1mm, making the power density at the focus more than 107W-108W/ ψ 2. The irradiated material is rapidly heated to the vaporization temperature and evaporated to form a small hole. When the beam moves linearly relative to the material, the small hole is continuously shaped into a slit with a width of about 0.1 mm. During cutting, add auxiliary gas suitable for the material to be cut to accelerate the melting of the material, blow away the slag or protect the cut from oxidation.
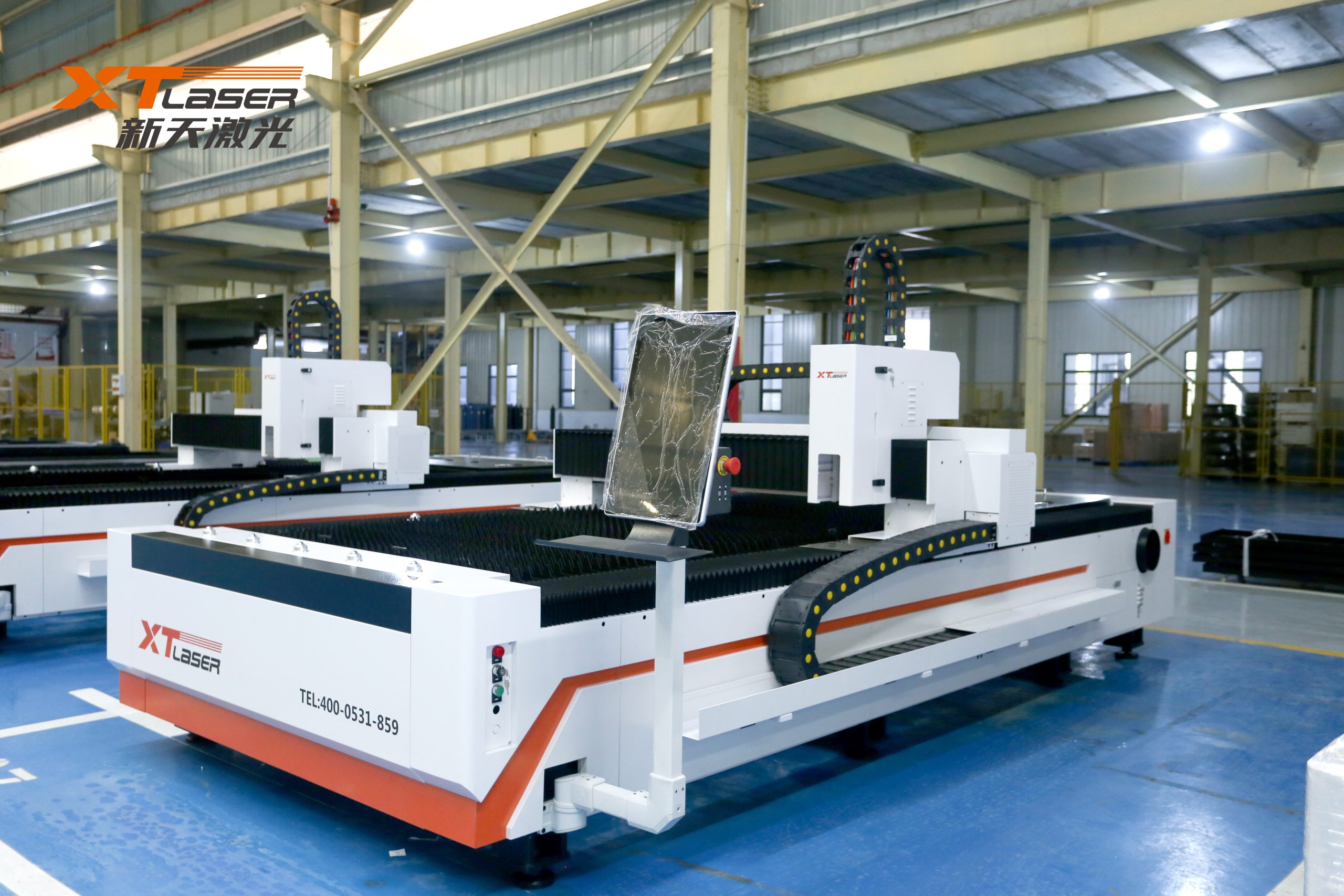
Many metal materials, regardless of their hardness, can be cut by laser without deformation. Most organic and inorganic materials can be cut by laser. Among the commonly used engineering materials, in addition to copper, carbon steel, stainless steel, alloy steel, aluminum and aluminum alloys, titanium and titanium alloys, most nickel alloys can be laser cut.
2、 Advantages of laser cutting.
● The slit is the narrowest, the heat affected zone is the smallest, the local deformation of the workpiece is minimal, and there is no mechanical deformation.
● It is a non-contact processing with good controllability. No tool wear, any hard material (including non-metal) can be cut.
● Wide adaptability and flexibility, easy automation, unlimited profiling and cutting ability.
Compared with traditional plate cutting methods, laser cutting has obvious advantages. Fast cutting speed and high production efficiency. Good cutting quality, narrow cut. Good material adaptability, no tool wear. Both simple and complex parts can be accurately and rapidly shaped by laser cutting. High degree of automation, simple operation, low labor intensity and no pollution. Low production cost and good economic benefits. The effective life cycle of this technology is long.
Compared with conventional processing methods, laser cutting also has obvious advantages. In the thermal cutting method, neither oxygen combustible (such as acetylene) cutting nor plasma cutting can concentrate energy in a small area like laser beam, resulting in wide cutting surface, large heat affected area and obvious workpiece deformation. Oxygen combustible cutting equipment has small volume and low investment. It can cut 1 meter thick steel plate. It is a very flexible cutting tool, mainly used for cutting low carbon steel. However, due to its large heat-affected zone and low cutting speed, the cut presents serious serration and serration. Therefore, it is rarely used for cutting materials with thickness less than 20 mm and requiring precise dimensions. The speed of plasma cutting is similar to that of laser cutting, which is significantly higher than that of acetylene flame cutting. However, its cutting energy is low, the cutting edge tip is circular, and the cutting edge is obviously wavy. During operation, it is also necessary to prevent the ultraviolet ray generated by the arc from damaging the operator.
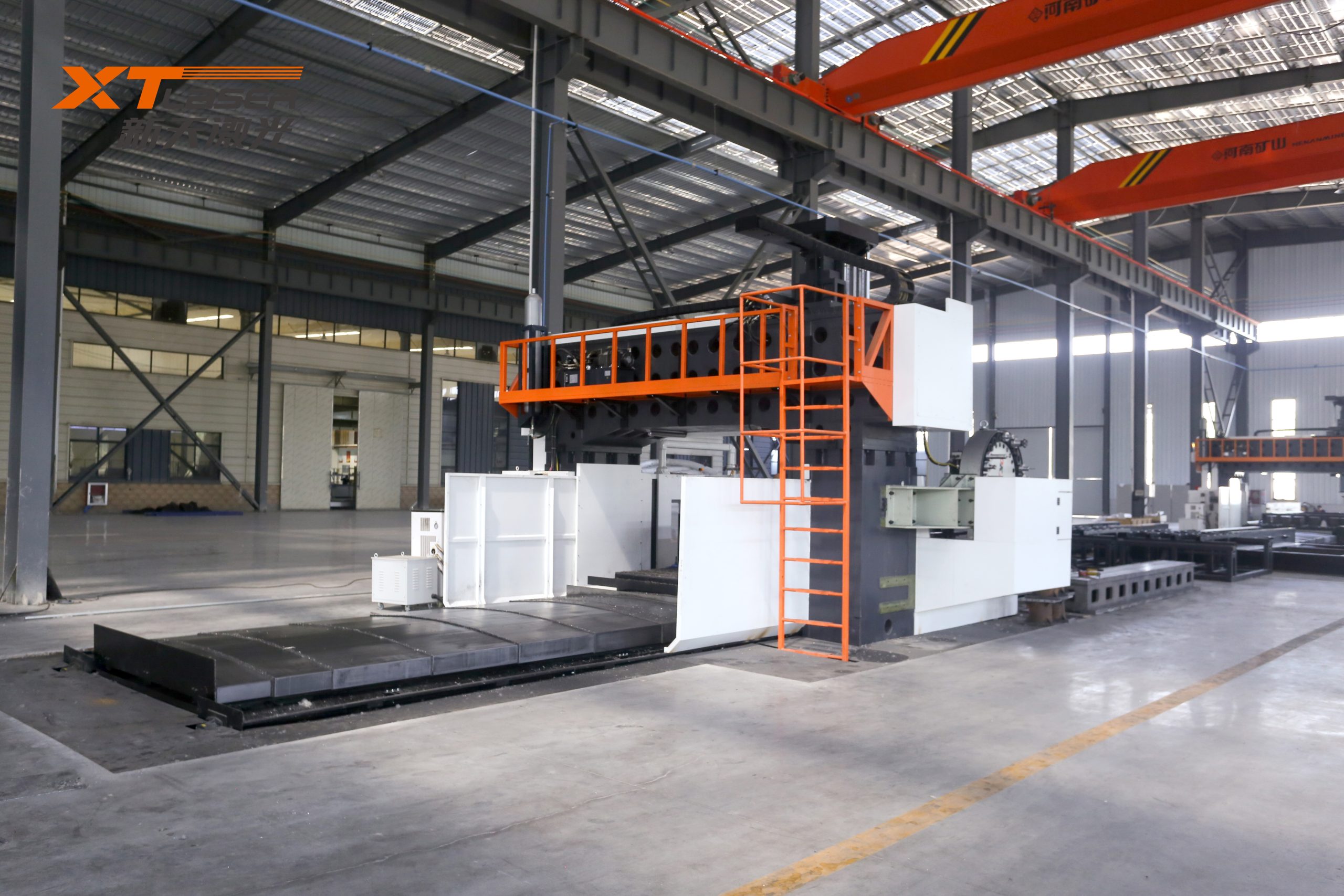
Compared with laser cutting, plasma cutting is slightly better because it is more suitable for cutting thicker steel plates and aluminum alloys with high beam reflectivity. However, laser can cut nonmetals, while other thermal cutting methods cannot. In the mechanical stamping process, using die stamping to produce large quantities of parts has the advantages of low cost and short production cycle, but this method is difficult to adapt to the changes in design, special equipment, long manufacturing cycle and high cost. For small and medium-sized enterprises, the advantages of laser cutting will be fully demonstrated. Laser cutting is conducive to the close arrangement and nesting of workpieces, which saves more material than die stamping, which requires more material allowance around each workpiece. For large and complex parts that need to be punched in sections, a punch is required to punch, resulting in many small shell-shaped cutting edges on the trimming, resulting in a large number of leftovers. For thin metal, sawing is adopted, and its cutting speed is much slower than laser cutting. In addition, as a flexible non-contact profiling cutting tool, laser can cut from any point on the material to any direction, which is beyond the scope of sawing. Electric spark or wire cutting is used for fine machining of hard materials. Although the incision is relatively flat, the cutting speed is several orders of magnitude slower than laser cutting. Although water cutting can cut many non-metallic materials, its operation cost is relatively high.