Three major fields of laser technology application in China
Laser marking technology, laser cutting technology and laser welding technology are three major fields of laser technology application in China
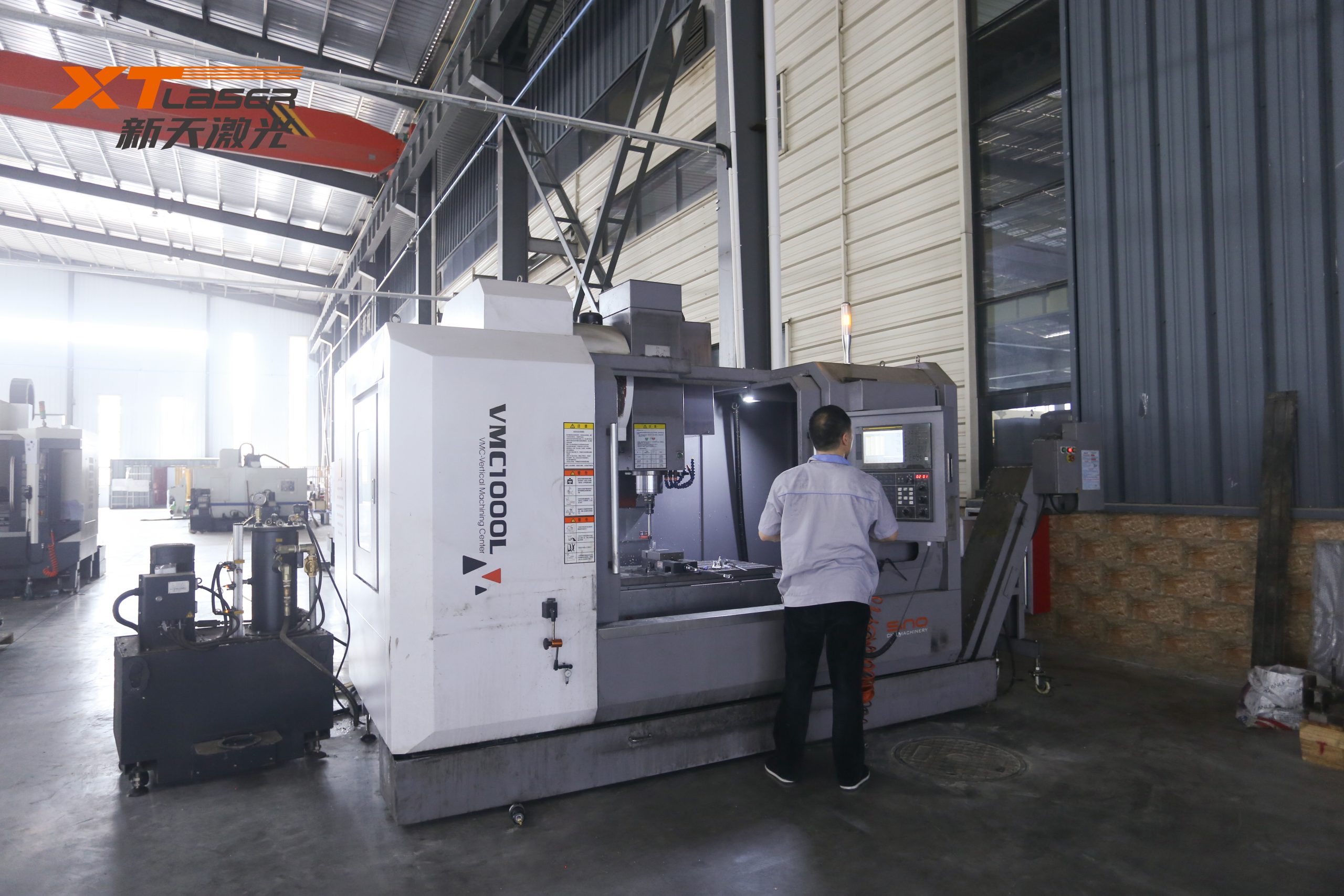
Laser marking technology
Laser marking technology is one of the largest application fields of laser processing. Laser marking is a marking method that uses a high energy density laser to locally irradiate the workpiece, vaporize the surface material or produce a chemical reaction of color change, thus leaving a permanent mark. Laser marking can print all kinds of characters, symbols and patterns, and the size of characters varies from millimeter to micrometer, which has special significance for product anti-counterfeiting. The focused ultra-fine laser beam is like a knife, which can remove the surface material of the object point by point. Its progressiveness lies in the non-contact processing in the marking process, which will not produce mechanical extrusion or mechanical stress, so it will not damage the processed object. Due to the small size, small heat affected zone and fine processing of the focused laser, some processes that cannot be realized by traditional methods can be completed.
The “tool” used in laser processing is a focus spot, which does not require additional equipment and materials. As long as the laser can work normally, it can be processed continuously for a long time. The laser processing speed is fast and the cost is low. Laser processing is automatically controlled by computer, and no manual intervention is required in the production process.
What kind of information the laser can mark is only related to the design content in the computer. As long as the drawing marking system designed in the computer can be identified, the marking machine can accurately restore the design information on the appropriate carrier. Therefore, the function of the software actually determines the function of the system to a large extent.
Laser cutting technology
Laser cutting technology is widely used in the processing of metal and non-metallic materials, which can greatly shorten the processing time, reduce the processing cost and improve the quality of the workpiece. Modern laser has become the “sharp sword” of “cutting iron like mud” in people’s imagination. Take the CO2 laser cutting machine of our company as an example, the whole system is composed of control system, motion system, optical system, water cooling system, smoke exhaust and air blowing protection system, etc. The most advanced numerical control mode is adopted to realize multi-axis linkage and laser speed independent energy impact cutting. At the same time, DXP, PLT, CNC and other graphic formats are supported to enhance the ability of interface graphics rendering and processing. The imported servo motor and transmission guide rail structure with superior performance are adopted to achieve good motion accuracy at high speed.
Laser cutting is realized by applying high power density energy generated by laser focusing. Under the control of the computer, the laser discharges through a pulse, thus outputting a controlled repetitive high-frequency pulse laser, forming a beam with a certain frequency and a certain pulse width. The pulsed laser beam is transmitted and reflected through the optical path, and focused on the surface of the processed object to form a tiny, high-energy density light spot. The focus is located near the processed surface, and the processed material is melted or vaporized at an instant high temperature. Each high-energy laser pulse will instantly splash a small hole on the surface of the object. Under the control of the computer, the laser processing head and the processed material move continuously relative to each other according to the pre-drawn figure, so as to process the object. The desired shape. During cutting, the gas flow coaxial with the beam is sprayed from the cutting head, and the molten or vaporized material is blown out from the bottom of the cut (note: if the blown gas reacts with the material to be cut, the reaction will provide additional energy required for cutting. The gas flow also has the function of cooling the cutting surface, reducing the heat affected area and ensuring that the focus lens is not contaminated). Compared with traditional plate processing methods, laser cutting has the characteristics of high cutting quality (narrow cut width, small heat affected zone, smooth cut), fast cutting speed, high flexibility (can cut any shape at will), wide range of materials, etc. Adaptability and other advantages.
Laser welding technology
Laser welding is one of the important aspects of the application of laser material processing technology. The welding process is heat conduction type, that is, the surface of the workpiece is heated by laser radiation, and the surface heat is guided to the internal diffusion through heat transfer. By controlling the width, energy, peak power and repetition frequency of the laser pulse, the workpiece is melted to form a specific molten pool. Due to its unique advantages, it has been successfully applied to the welding of small parts. The emergence of high-power CO2 and high-power YAG lasers has opened up a new field of laser welding. Deep penetration welding based on keyhole effect has been realized and has been increasingly widely used in mechanical, automotive, steel and other industrial sectors.
Compared with other welding technologies, the main advantages of laser welding are: fast speed, large depth and small deformation. It can be welded at normal temperature or under special conditions, and the welding equipment installation is simple. For example, when a laser passes through an electromagnetic field, the beam will not deflect. The laser can be welded in air and some gas environments, and can be welded through glass or materials transparent to the beam. After laser focusing, the power density is high. When welding high-power devices, the aspect ratio can reach 5:1, and the maximum can reach 10:1. It can weld refractory materials such as titanium and quartz, as well as heterogeneous materials, with good effect. For example, copper and tantalum, two materials with completely different properties, have a qualification rate of almost 100%. Micro welding is also possible. After the laser beam is focused, a very small spot can be obtained and can be accurately positioned. It can be applied to the assembly and welding of small parts in large-scale automatic production such as integrated circuit lead, watch hairspring, picture tube electron gun, etc. Laser welding not only has high production efficiency and high efficiency, but also has small heat affected zone and no pollution to the welding point, which greatly improves the welding quality. It can weld parts that are difficult to contact and realize non-contact long-distance welding, which has great flexibility. The application of optical fiber transmission technology in YAG laser technology has made laser welding technology more widely promoted and applied. The laser beam can be easily divided according to time and space, and can be processed simultaneously and at multiple stations, providing conditions for more accurate welding.